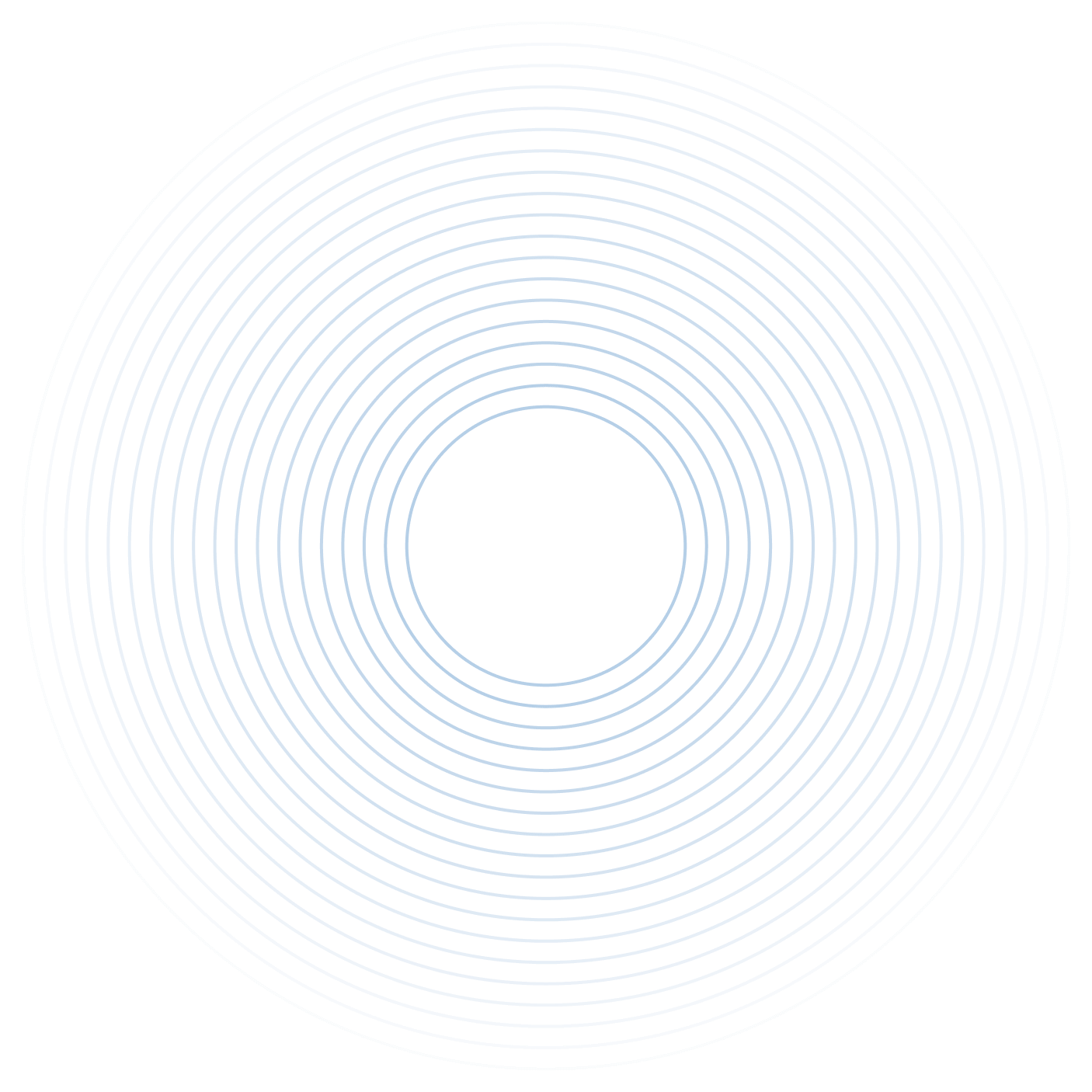
1. AI與大數據導入跟SPC關聯 ? 製程參數與檢驗結果該如何應用AI大數據才能有效提升良率呢 ?
SPC 是將大量數據應用統計分析手法找出規律,如果能將管制項目找出其特性,便可應用AI演算法在大量數據中快速找出相對應的規律。所以這兩者是相輔相成的,SPC可以說是品質系統引入AI的前置條件,有了SPC的經驗與統計分析結果,才可驗證與判斷導入AI是否有真實效果。
同時SPC在成本上也有更大的優勢,用在檢驗管制項目Q最好是SPC,而用在製程參數P的大數據分析可引入AIQ或是其他系統,在智慧工廠的範疇內,P&Q 掌握好才可有效提升良率與降本增效。
2. SPC 對品管有何幫助 ?
SPC 能利用統計的知識,以共同的語言(數學),讓使用者輕鬆的了解現在品質的真實狀況,更可利用量化的數據與適當的管制圖,找出真正的異常,以科學化的方法,有效且具體改善品質。
3. SPC 常用於品管的那幾個階段 ? 有那些需注意的事項 ?
SPC可用於品管的任一階段,但最常用在IPQC與PQC,在導入 SPC時,最容易犯的錯誤就是誤以為只要導入SPC軟體,就能解決問題,或是導入SPC軟體跑一些數據給客戶交差了事就算了。
因此除了要對SPC的導入有正確的觀念之外,最重要的是要有正確的執行觀念與專業的輔導團隊,再加上具體的執行步驟方能有效。
4. 如何比較 SPC 軟體系統的好壞 ? 如何確保導入的成效 ? 專業的輔導團隊如何尋找 ?
SPC 軟體系統的好壞可以從三個方面來看:
實用性 :
先確定您要的是管理性為主或是分析性為主的SPC,分析性的如MINITAB均可作專業統計上的分析,惟須有同樣專業的人員操作,否則分析出來的效果與預期可能完全不同。
這類的統計分析軟體往往根據的是一個單一專案或是獨立數據集來做分析,比如實驗室的某個專案或是研發RD的新產品特性實驗研究數據集。管理性與分析兼具的如中方SPC系列,可針對生產檢驗的大量資料,做系統性的管制與ALARM。除可連接各種不同的自動化量測儀器增加量測的效率,準確性及節省量測的人力,完整管制圖的功能與參數的豐富性與正確性可增加品管判讀的速度,串接ERP、MES或是ALARM MAIL、三色燈等應用。適合用在整廠實務上的規劃與應用。
擴充性與服務 :
如是否為原廠,可否配合工廠軟體環境變化而成長?如資安要求、TLS2.0等;是否有網路版本乃至支援VM,支援的資料庫格式與公司的MES、ERP 等系統是否可連接或拋轉資料,工廠附近是否有服務據點可在需要時做儀器連線、問題排除配合與其他自動化等可能的配合,是否有兩岸甚至東南亞等其他國家的在地服務?如客戶有大陸廠,是否有大陸分公司可提供當地服務,距離客戶地點多遠?服務人員的專業性如何?SPC是一套需要專業服務與專業軟體的系統,價格雖然重要,但買了一套沒有服務或專業性,擴充性或是無法配合公司環境如WIN11,OFFICE2023,MSSQL2023等成長的團隊,不但無法支援,同時會限制公司的發展,甚至變成絆腳石。
口碑與支援 :
公司規模與歷史,同時過去這套系統曾服務過那些客戶?使用情形如何?軟體廠商往往5-10年就會倒閉或收攤,闖過每十年一次大浪的有口碑或是已經有多家大型客戶使用的系統較不會有問題,大浪掏沙後留存下來的系統經過歷史的考驗,系統穩定性與自我優化淘汰的能力夠優秀才能存活。另外團隊能力方面,最好是員工有10年以上經驗,這樣的輔導與技術或規劃資深工程師,規劃出來的系統實用性一定較強,如要求他們來展示,可審視其服務水準與是否有技術管理制度,通常優秀的專業公司在規劃上會有一套評鑑的程序 ,如是新進的廠商要求公司合作開發或低價且任何狀況都能配合或是輕諾,往往是找人作他們的白老鼠,結果通常是勞民傷財導入失敗,同時軟體商如規模太小在研發的持續性與風險通常較高,因此找口碑好,支援上可適合公司各個成長階段的合作夥伴會較有保障。
5. SPC 有試用版嗎 ? 試用有用嗎 ?
SPC試用先要了解試用意義為何?通常是不知有那些功能 , 且自己怕買錯,想要自己使用看看再說。但是現在SPC或其他品質系統往往已經發展為一個系統,需要建立基本資料或是有些前置條件,才能有效使用,如果是已經有具體的需求或功能要求,可以請廠商協助建立具體測試環境,並將模擬數據請其幫你導入系統後,請廠商工程師模擬給我們看是否可滿足需求,如檢驗報告等。要是用它必須對它有全盤的了解,否則只是一知半解,反而會評估錯誤,因此建議一定要請廠商來說明他們的系統架構與使用方式,如果合適,再提出試用要求與試用計劃,這才是良好評估的方式。但試用不一定有用,因為通常試用者並不會真正正確的使用,還是由系統商作完整的教學較合適。
6. 6σ是什麼 ? 用6σ聽說可以改善製程品質 , 是真的嗎 ?
6σ是Motorola 提倡品質改進的一個方法,如果達成,不良率可以降低至3.4PPM,亦即使用此法可將現有3σ的99.73%良率大幅提昇,但6σ程序目前有GE,Motorola各有其不同程序與方法,同時牽涉從設計研發的起源開始改善DMAIC,至於在 SPC 部份來說,SPC是所有改善品質的基礎。不管做哪一類型的改善,以製程上角度來說,SPC 是一切改善的基礎,因此如有人說6σ可以改善製程品質僅為概論說法 , 6σ改善品質需要許多的配套措施方可以有機會達成,並不是某些廣告詞所說的像萬靈丹一樣,但是如果有系統的導入6σ的組織與手法,加上貫徹改善的決心與執行力,將可以大幅改善生產效率與品質,非僅提升製程品質,更能夠有效減少浪費增加全公司的競爭力。
7. 貴公司SPC 所使用的公式為何 ? 如我的客戶要知道 , 可以嗎 ?
在本公司軟體的說明欄會附使用的公式,且都有出處,購買本公司SPC 軟體者,在操作手冊的附錄中也有。
8. 貴公司的SPC需求電腦配備為何 ?
SERVER 需要CPU在3.2GHZ RAM 32GB 以上(以資料庫為 SQL 而論,硬體成本在 NT$ 5-6 萬左右) 因本系統做過優化,以 300 萬筆資料蒐尋 3 萬筆資料為例,實測速度約8秒鐘。更有針對大數據的各種配套快速運算與QIR等客戶定時自動搜尋日周月季報表,發送自設格式報表給各主管或是傳送到MES,ERP做BI看板的品質來源。
9. 貴公司的SPC 可與本公司的儀器連線嗎 ?
只要有輸出的儀器均可,基本上小量具免費,但其他儀器依狀況收費。
10. 要將 SPC 系統導入成功 , 我們公司要準備哪些事項 ?
這個問題非常好也非常重要。要做好 SPC 系統的導入,有幾個要點:
1、各廠所作的產品,收集品管資料目前的架構與檢驗站。
2、目前收集資料所用的方式為何?。人工,excel,其他系統請說明
3、各站檢驗的頻率與收集的樣本數及母體,請詳盡介紹。
4、各廠區收集資料檢驗的標準作業程序與品質工程表。
5、各廠的IQC & OQC 報表樣本 。
6、各廠目前各站的檢驗人員有多少?受過訓練否?
7、各廠目前使用的量測儀器為何?自動化程度為何?。
8、各廠品管人員想看到那些定時報表?常用的有那些?
當遇到問題時,異常如何處置?
如您對上述問題有疑問,請洽本公司服務團隊,我們將以專業的服務態度為您做進一步說明與輔導
11.WEB SPC 在中方科技定位 ? 與原有SPC系統有何差別 ?
此版本是為行動輸入而設計,不管Android、iOS或是Windows 平板或是手機,都可以帶此版本巡檢輸入,在許多不方便設立電腦收集檢驗資料的位置,用此版本可以讓使用者輕鬆收集即時數據,不需要紙本輸入後再拿回位置重新打字輸入電腦。此版本介面簡單易懂,適合第一線人員快速學習輸入,更有打開設計圖,讓第一線使用者正確輸入管制項目內容。
與原有SPC系統是相輔相成的作用,中方SPC有業界最豐富的自動化收集與最多樣的分析圖表,自動警訊與串接各項不同系統的功能,因此WEB SPC輸入的資料完全可與現行SPC系統整合,可將其視為另一種直接輸入SPC的來源。
12.WEB SPC 可支援多國語言嗎 ?
可以,此版本支援響應式網頁,EDGE或是CHROME等都支援,如果用CHROME瀏覽器,可直接使用其支援多國語言切換的功能。
13.WEB SPC 可離線輸入嗎 ? 可給供應商輸入直接連到中心廠嗎?
WEB SPC 有離線輸入模式,但須要有相對應配套措施。畢竟離線的時候要輸入那些檔案與管制項目,會否與原有系統衝突等需要規劃與設定,先後順序也有可能造成連線後OOC的誤判,這些都要考量進去。
中心廠若需要給供應商輸入製程資料連線到中心廠,用現有系統或是WEB 都是可以的,作法為在SPC系統中設定某一群組為供應商群組,給供應商特定帳號定義輸入與觀看查詢權限只能看到此群組而非中心廠其他群組,然後將此群組邏輯隔離在其他群組外,若擔心可專門切分一個小SERVER ,定義此對外DB設定相關供應商群組,加上防火牆與資安加密等。都可以做到。但如果是要供應商的COA上傳而非即時製程資料,這種情況建議考慮我司的SQP系統串接中心廠的SQM系統,因為對供應商關係不一定只有SPC,供應商抽樣流程、供應商評鑑、供應商有效文件管理等等都是需要考量的。簡單的說,若需即時輸入製程數據,WEB SPC是最佳選擇;若是進行供應商管理、文件監控與抽樣流程,則推薦使用SQP/SQM
14.WEB SPC 可與ERP或MES串接整合嗎 ?
可以。但基本上必須在連線狀態下,透過MIC模組串接配套才不會有問題。
15.WEB 版的資安如何保障 ?與貴司原有系統資安差別如何?
WEB 版出版時都有經過HTTPS SSL的測試,傳輸安全性與資料加密也都有做,支援內網與外網,但資安部分還是要靠企業原有的資安防護。中方原有系統為CS架構,必須安裝CLIENT SPC才可以跟SERVER相連,此種封閉式架構資安本就高於WEB,何況CS之間的通訊都有符合TLS1.2的加密通訊。若之後有更多資安規範,我司也會改程式符合最新規範。
16.WEB SPC 需要那些軟硬體環境
SERVER 要有標準的IIS 架構才可以,使用端用一般手機、平板、電腦都可以。詳細說明如下
【伺服器環境】
• IIS架構:確保伺服器支援 Internet Information Services (IIS),並符合最新版本。
• 作業系統:通常建議使用 Windows Server(如Windows Server 2016或以上)來提供穩定的運行環境。
• 硬體需求:伺服器應具備足夠的 XEON CPU、32GB RAM與1TB以上儲存空間,以應對大量數據處理與使用者存取需求。
【使用端環境】
• 瀏覽器支援:WEB SPC應支援 Chrome、Edge、 Safari 等現代瀏覽器,以確保最佳相容性。
• 裝置支援:可在 手機、平板、筆記型電腦與桌上型電腦 上運行,並確保不同解析度下的介面適應性。
【網路與安全性】
• 網路連線:建議使用 穩定的網路環境,如企業內網或VPN,以確保數據傳輸安全。
• 資安機制:應支援 HTTPS加密、TLS 1.2,並搭配 防火牆與存取控制 來保護系統。
【系統整合與擴充性】
• 資料庫支援:可與 SQL Server 整合,以確保數據存儲與查詢效能。
• MIC或API串接:若需與 ERP、MES或其他系統 整合,應提供 API或相關介面。
17.貴司系統支援雲端或虛擬主機嗎 ?
支援,SPC系統DB為MS SQL,SQL系統支援AZURE,AWS等系統都有上線實績。通常建議如果有多區域廠區(如兩岸、東南亞等)或是有些廠區會設立到美國或墨西哥等,都可以考慮雲端系統。但要注意的是頻寬與系統穩定性,當然這就並非我們應用程式廠商所能決定的。
18. SPC應用問答(上)
1.現在全檢當道,是否採用全檢就不需要用SPC?全檢可以改善品質嗎?
導入SPC有兩種用途,一種是利用抽檢了解產品品質,這種全檢可以取代。
一種是預測未來一段時間的產品品質趨勢並且推定多久後會有異常,提供當下調整製程的訊號。提升良率。
檢測真正的目的是讓不良不再一直發生,積極目的是品質資訊發給前段製程讓前段製程可以即時改進以免不良一直發生。 這也是工業4.0中品管的積極意義所在。
2.SPC是以常態分配為基礎,如果管制項目數據不屬於常態分配,是否就不適用SPC?遇到這種情形該如何是好?
是。遇到不符合常態分配的管制項目,可判定其特性後藉由適合該特性數值轉換將其數值轉成常態分配後再使用SPC。
3. 自動化可省下人力,但也聽說有效益不佳甚至高額損失的例子,我們應該如何面對?
先做自我診斷,是減少人力 ? 還是增加效率 ? 自動化目標是增加機器人生產,還是收集機台參數,還是串聯各資訊系統(如CIM),不同的目的造成不同的方案,建議先有整體規劃,再分成不同階段導入,最好IT主管可以全程參與,至少在資訊系統的串聯上不會前後矛盾。
4.工業4.0對品管有何幫助?我們要如何應用工業4.0、大數據、雲端等技術提升生產力與品質競爭力?
工業4.0可以應用在許多領域,但以品管角度來看,工業4.0 最重要的是可將製程參數與品質結果相串聯,將檢測數據經過運算後的結果即時反饋到製程參數的調整,讓不良品可有效且即時的降低,而不是由人員依照經驗猜測無依據的調機。當未來資料收集的越來越完整,透過人工智慧與更多元的參數模型,將能有效地建立更有效能與效率的生產模式。
5.聽說投入巨資導入工業4.0的公司不少,我們在有限成本下該如何因應呢?
錢多錢少各有作法,首先應先內部了解你們如果要導入工業4.0,想要有哪些具體目標,不要人云亦云,也不要將目標建得模模糊糊,具體目標指的是能量化且可評估指標(如希望增加生產效率20%),初期建議先建立小目標。這樣的投入與產出比較可以有具體的評核標準。
6.台積電針對供應商做特殊SPC管制要求,該如何規劃應用?對品質控管有幫助嗎?
是指在真實製程條件下,先進半導體製程建構之異常發生的模型(如與前一週生產檢測數據比較,OOC發生數高於平均則為異常)
這種模型並非一般統計上的檢定,但在製程實務上確實能偵測品質異常,尤其是少量多樣的自動化生產,使用類似的模式
將自動收集檢測數據自動判定,往往能第一時間抓到生產製程變異,對供應商的壓力更大但是品質提升的速度也會更快。
19. SPC應用問答(下)
7.改為FMEA_VDA新版與CP新版已經陸續於2019.5&2024.3發布,汽車與電子業客戶都要求FMEA-CP串接,CP-SPC串接,該如何導入才能符合客戶需求又能發揮真實效益 ?
ANS : FMEA新版自2019年以來,中方開發符合FMEA新版之軟體系統,並在後續經由日X光、欣X電子、南亞X路板、台灣汽車XX等客戶上線順利,符合國際車廠福X、GX、BENX等車廠的要求。FMEA與CP的串接經過2022-2025年各階段陸續研發,已經從初期的專案對專案串接,進步到條與條的串接,並經由南X、楠梓X等客戶驗證通過,所以這塊可以相信中方的專業輔導經驗,從如何建立公版與專案、串接的設定與匯入舊資料,AP辭庫與FMEA、CP專用各類詞庫的建立與應用。圖表分析與客戶報表的產出,都需要有豐富經驗的輔導顧問與強有力的軟體工具,才能符合客戶需求又能展現真實效益。同時,現今地緣與資安要求,過去有些代理大陸軟體,輔導廠商要求客戶研發FMEA機密上網輸入,雲端資料庫在大陸,陸續已經被美方客戶警告,這點也會有所影響。如中方系統伺服器與輸入端都在客戶端,資料沒有外洩疑慮,是較佳選擇。資料庫架構與快速建構系統,舊資料匯入功能可讓客戶快速建構FMEA_CP_SPC系統,全文檢索搜尋與自設報表匯出可以讓使用者有效使用已經輸入的資料並組合成客戶需要的範例,更能真實有效將工廠品質智慧應用到真實活動中,故可發揮最佳效益。
8.APQP、PPAP、MSA、FMEA、SPC五大核心工具應該如何串聯才能讓品質提升?現有ERP&MES又該如何整合才能讓效益發揮到最大?以上系統又該如何自動化,有合適且有成功經驗的架構嗎?
中方有QRP系統與針對五大核心工具導入的套件包,可以用此當作入門基礎。都有成功案例。
9.導入品質系統往往看不到成效,應該如何導入才能看到成效?
訂定短期內可具體達成的目標,如自動化連線或是例行性品管報表自動產出,或是找中方顧問規劃。
10.客戶要求第二階供應鏈SQM管理加強,要如何做才能滿足客戶需求?
先就供應商拉出核心供應商(供應最核心物料或是最大量物料的供應商),並將相應的收料計畫檢討 或是找中方顧問討論針對各種供應商的管理計畫,以此計畫跟客戶溝通。
11.聽同業說SPC-QIR自動智慧報表可以幫助決策順暢,請問原因為何?
因為中方SPC-QIR可自設各階段(如當日、當周、當月等)的管理報表(如by料號、機台、班別、批號、部門….)自動發送給相關管理主管(可自訂),在某些狀況下甚至可專案製作如每小時Cpk、良率/不良率、OOC/OOS…與生產看板結合。
這樣的功能就已經將品質管理從一般管理升級到自動管理,讓決策即時與順暢。
12.中方的品質系統有WEB、CLIENT-SERVER、也有C語言接生產機台、PLC的系統,請問設計理念與為何要這樣規劃呢?
因應安全性與方便性,還有機台連線的底層需求,中方會針對不同的需求以不同工具開發,這樣在效率、長遠性與擴充性會最佳,雖然這樣開發較辛苦,但考量到工業環境的長遠需求,還是以此方式會較適切。
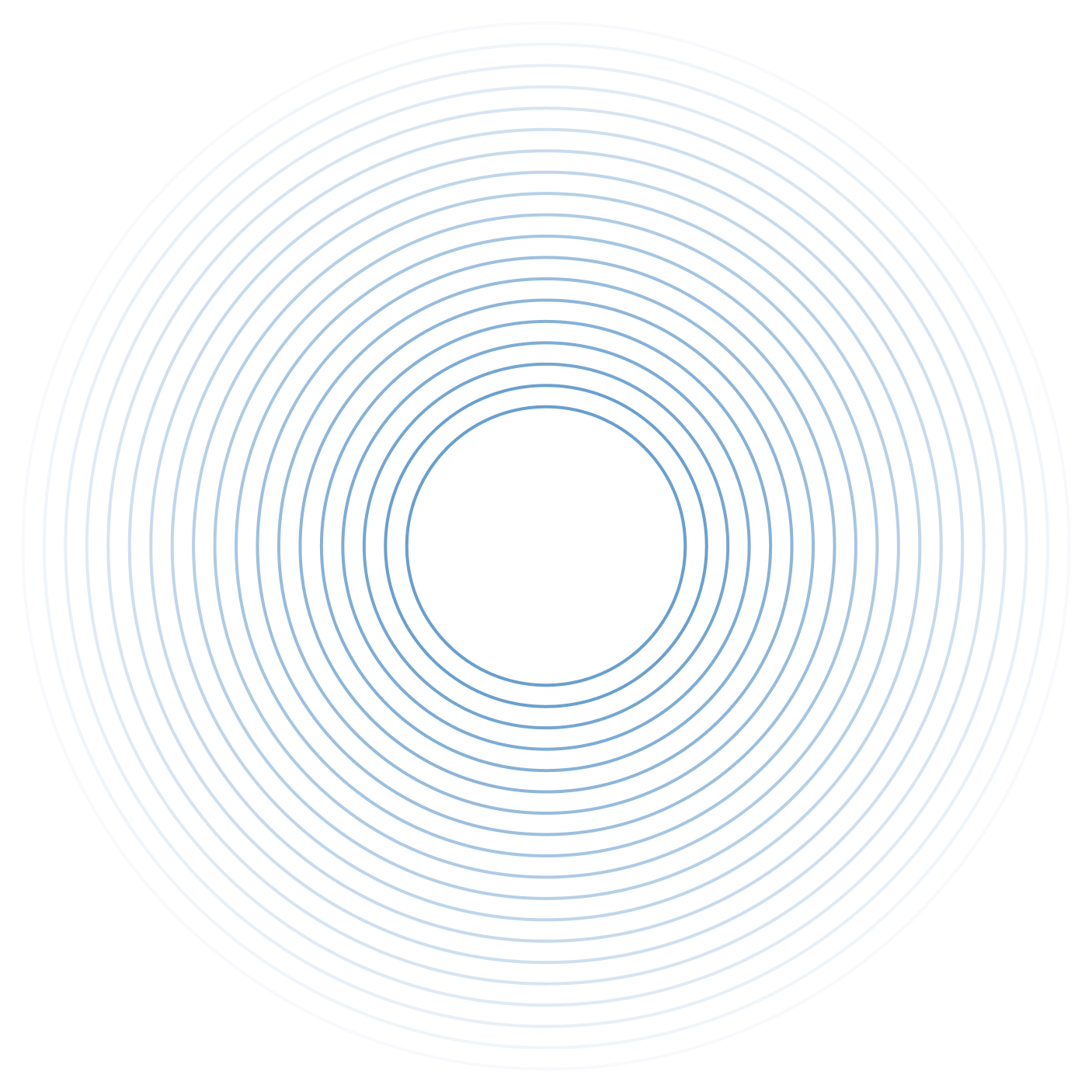
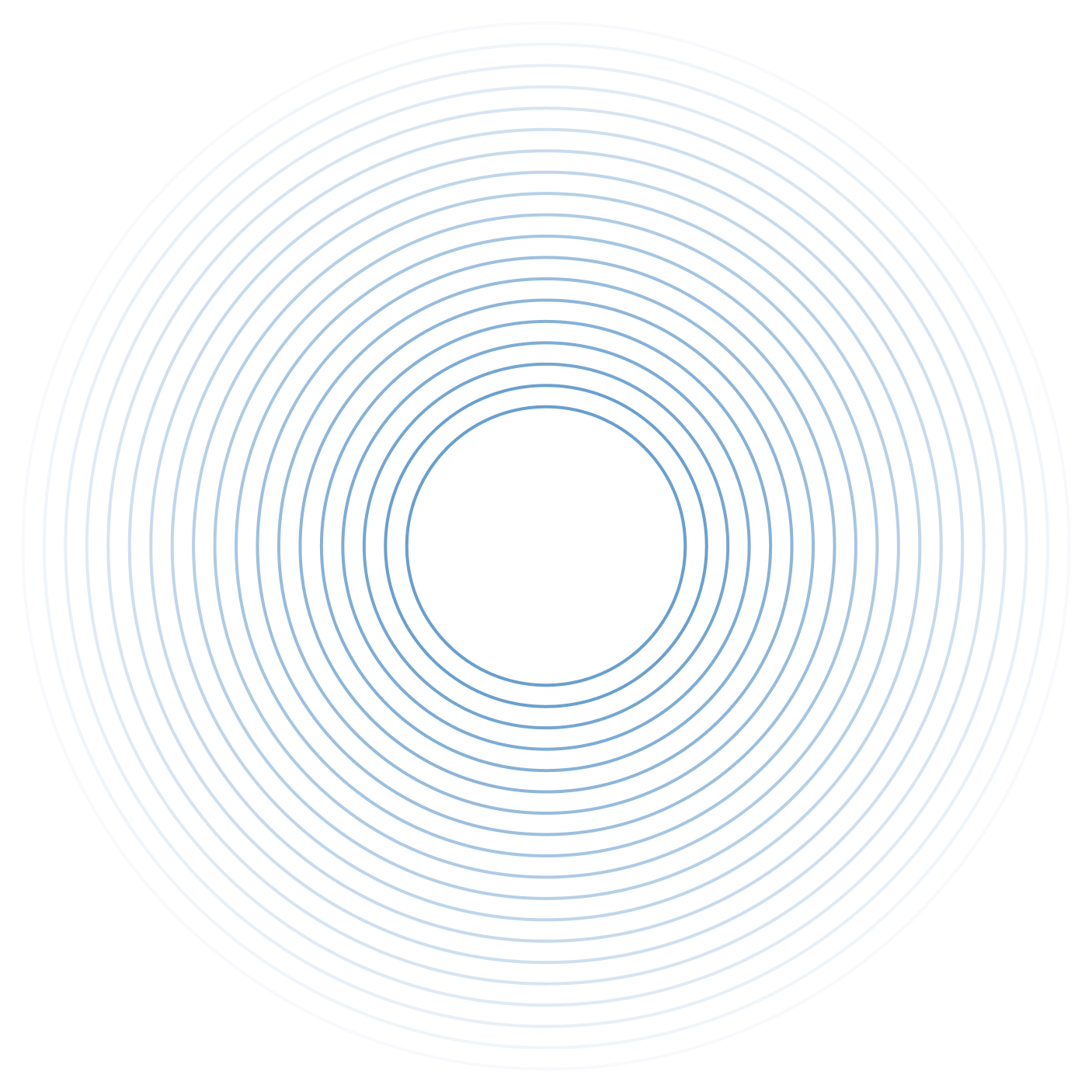